We talk about the need for standardisation and transferability all the time, but what does this mean and what do we need to do? ECITB Director of Operations Andy Brown gives some thought on this important subject area and, actually, how difficult it is to achieve.
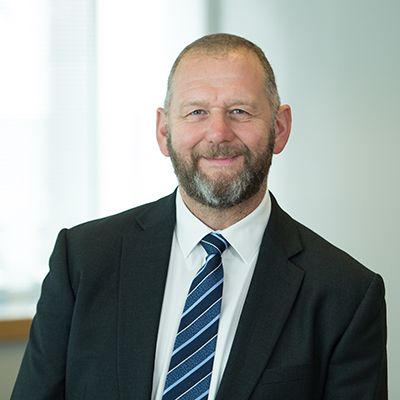
Andy Brown – ECITB Director of Operations
So what do we mean by standardisation? Standardisation ensures that the training delivered and the qualifications, awards and tests that demonstrate attainment, are based on industry or national standards.
And why do we do this? In the area of training, it’s a measure to see if an individual has reached the correct, agreed level of knowledge or skill, and in the area of qualifications, awards and tests, we’re checking that they have acquired the correct knowledge, skill and sometimes behaviours.
Most of what we do at the ECITB is driven by trying to get the industry to reach the standards set and that these are the accepted standards. It is probably a well-forgotten fact, but the ECITB is a Standard Setting Body, recognised for being the guardians of the industry National Occupational Standards (NOS). The NOS come from industry and set out the performance criteria and knowledge requirements for a given occupation. These NOS in effect, form the industry training and competence framework for craft and technician disciplines, which include project controls and design & draughting standards. These standards enable us to create VQs, training programmes and technical tests.
Similarly, the ECITB drives standardisation through the issue of the CCNSG (Client, Contractor National Safety Group) Safety Passport, which is the recognised passport for gaining entry onto most onshore industry sites. We also do this through our grant offer, as much of the funding is for national qualifications or industry recognised programmes, such as Non Destructive Testing and Project Management.
The use of standards help regulate the recognised competences and attainments of the engineering construction workforce, which in turn supports the movement of workers with valid certifications in the recognised standards between industry sectors. This transferability reduces unnecessary training costs and duplicate testing. Of course, training and testing to agreed standards also ensures safety and productivity on sites and in engineering offices.
Making sure everyone works to a standard should therefore be very easy. However, there are several significant barriers to this.
Clients or asset owners often set the safety requirements for their sites long before any contractors are involved. If this happens, they can require different passport schemes to those already held by the contractor, this adds cost as the contractor has to acquire the stipulated passport.
So what? I hear you say. Improving standardisation and therefore aiding transferability is a significant part of the ECITB strategy and vision for the engineering construction workforce in the future. In a resource constrained industry, we will have to mobilise workers from oil and gas sector to net-zero projects, including offshore wind, and into nuclear new build. We need to do this in as cost efficient way as possible otherwise the cost of the projects – and therefore the risk to investment – goes up.
We are already addressing this in several ways for example our new entrant programmes are set sagainst standards, the Nuclear New Build Competence and Qualification matrix uses industry and national standards, and the Project Management Mentoring programme is based on industry project management standards.
However, I want to highlight two other ways we are doing this, namely through our Connected Competence and ACE Renewal programmes, particularly as these programmes have the potential to realise the biggest benefits.
Connected Competence is the standardised testing of basic trade competence where nationally recognised schemes do not already exist. It sets the blueprint for standardisation of technical competence assessment in as cost efficient manner as possible and will inform the way forward for renewal of the ECITB ACE scheme, which is for individuals who hold an ECITB vocational qualification and a valid CCNSG safety passport.
This applies to most of the craft and technician disciplines used in an engineering construction project. By agreeing a standardised set of tests for all contractors to use we can remove the duplication of testing that occurs as workers move from contractor to contractor.
Now, Connected Competence has been in development for some time. And as the programme of work has developed, the requirements have changed leading to additional complexity and the need for realising cost benefits becomes an ever increasing driver. Initially, it was envisaged that an agreed suite of tests delivered in a centre was all that was required. However, at this stage there was varying buy-in from contractors who could see that sending all of their workers to test centre was adding cost. To address this, the industry was brought together under a leadership council to align to a common set of objectives.
Having aligned the contractors, the next barrier that needed to be overcome was getting buy-in from the asset owners. Without the clients mandating the requirement, there was no leverage for the contractors to comply, which undermines the whole standardisation piece. There are now several clients sitting in the council, aligned to and supportive of Connected Competence. However, just as you think there’s alignment and client mandate, the price drops out of the market and cost becomes an even greater driver. This has created the need to configure the tests against work scope and provide a digital means of assessment and online knowledge-only tests that do not require workers to travel to offices and test centres.
This is where we are at the moment with Connected Competence. Work is ongoing and we know industry feels the rewards are worth it as they continue to commit resources and provide assets to allow a pilot assessment of the tests, hardware and software. Of course we have committed significant resource through the product managers, R&D, IT specialists and a dedicated Project Manager. The prize will be worth the effort as success with Connected Competence will feed into onshore testing and we hope form the basis of the All Energy Skills Passport of choice. This is significant as current users of Connected Competence mobilise their workers on multi-sector sites. We have the backing of major players in oil and gas at the moment and we need to keep the momentum going to deliver cost efficient standardisation of competence in energy transition too.
Standardisation and transferability sounds so easy…